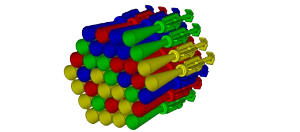
-
StatusOngoing
-
Status date2024-11-20
-
Activity Code5B.182 P2
Describe in less than 200 words the objectives of the project.
The satellite communication market is evolving towards medium-volume production of antennas and associated front-ends. Indeed, in GEO applications, complex focal plane arrays of hundreds of antenna-feed chains and BFNs are required to implement Tbps VHTS systems. In LEO and MEO applications, constellations of several hundreds or even thousands of low-cost small satellites are already in operation or will be deployed soon.
In this framework, additive manufacturing (AM) technologies are being steadily investigated and exploited for the development of RF equipment for satellite communication payloads. Indeed, AM technologies provide several advantages with respect to conventional machining, among which are free-form capability and fit-for-purpose design. These two specific aspects of AM enable the integration of different functionalities in a single monolithic part, thus reducing the number of parts, costs, lead time, and MAIT activities.
The present project aims at developing through AM a monolithic K/Ka-band dual-circular-polarization antenna-feed system with integrated RF, thermal and mechanical functionalities, intended for GEO High Throughput Satellites.
Additive manufacturing technologies offer several advantages in the development of highly integrated RF systems with additional functionalities. However, they also present critical aspects in terms of dimensional accuracy and surface roughness, when RF equipment working at K/Ka bands and in dual-circular polarization are targeted. In this view, one of the main challenges of the present project deal with the RF, mechanical and thermal co-design of the antenna-feed system capable of minimizing the impact of the manufacturing process on the performance. In parallel, challenges apply also on the manufacturing process in order to optimize the production parameters for the intended application.
High Throughput Systems (HTS) are among major trends in the satellite communication market, thanks to their potential aggregated capacity of Tbps. This goal is achieved exploiting dense focal plane arrays composed of hundreds of complex antenna-feed chains. In this context, AM is a convenient solution for the integration of complex structures that implement different RF functionalities in a single part, thus avoiding problems as connecting flanges, screws and passive intermodulation product generation. A further aspect concerning the benefits of the present product for space applications is the integration of radiofrequency, thermal and mechanical characteristics, thus reducing the number of parts, costs, lead time, and MAIT activities.
A multi-beam regional coverage HTS system operating in K/Ka bands was selected as a reference scenario for the development of the antenna-feed chain. The coverage area is divided in 111 cells with a footprint of 0.34 deg. At system level, the antenna farm requires an antenna directivity within 47-50 dBi and a bandwidth allocation, for user beam, of 600 MHz (within 17.7-20.2 GHz) in Tx and 440 MHz (within 27.5-30 GHz) in Rx. Using a single-feed-per-beam architecture in a classical four-color space diversity scheme, the antenna-feed chain has to provide dual-circular polarization capability and two frequency channels in both Tx and Rx bands. By considering appropriate frequency margins, operative bands of 18.5-20 GHz in Tx and 28-29 GHz in Rx were considered in the present study. When considering a classical 3.2 m reflector with a f/D ratio of 1.25and clearance of 0.8 m, the feed-horn aperture has to be around 43 mm. In terms of scattering parameters, the antenna feed-chain should present a return loss and port-to-port isolation in polarization better than 20 dB, isolation in frequency higher than 40 dB, insertion loss lower than 0.5 dB, and cross-polarization lower than -30dB.
The K/Ka-band dual-circular-polarization antenna-feed chain developed in the present project consists of a smooth-wall feed-horn and an asymmetrical feeding-network.
Since a dense focal plane array is considered, the relevant feeding network has to fit within the radiating aperture of the feed horn. Moreover, it was considered the additional goal to minimize the transversal dimension of the feeding network to make feasible its potential application to arrays with smaller lattice steps. Indeed, asymmetric configurations lead to very streamlined geometries, compatible with lattice steps of the focal-plane array in the order of 20 mm, although at some expense in terms of performance (primarily, port-to-port isolation in polarization and XPD). To understand the applicability of these configurations, three different architectures were investigated.
The mechanical design of the EM integrates the adapters towards the standard measurement setup. The design of the thermal circuit integrated in the feeding network was carried out by considering a requirement of thermal dissipation equal to 2.5 W. After a trade-off study and considering the minimum tube dimensions, a Mechanically Pumped Fluid Loop (MPFL) system was selected.
The project plan consists of one phase, including the following milestones:
-
Requirements Review (RR), focused on requirements at system, antenna and antenna-feed chain level, regarding RF, thermal and mechanical aspects.
-
Mid-Term Review (MTR), focused on the preliminary RF design of the antenna-feed system and bread-boarding of key building blocks.
-
Critical Design Review (CDR), aimed at the consolidation of the RF, thermal and mechanical co-design and additive manufacturing route of the EM.
-
Test Readiness Review (TRR), focused on manufactured EM, test plan, and measurement setups and procedure.
-
Test Review Board (TRB), aimed at the discussion on the comparison among predicted and measured performance of the EM, including RF, thermal and mechanical responses/properties.
-
Final Review (FR), including all the activities carried out during the project and discussion on lessons learnt and follow-on activities.
The project was successfully completed. Indeed, the tests performed on the EM confirm the validity of the RF, thermal and mechanical co-design and manufacturing approach and pave the way for a continuation of activities aimed at obtaining a higher TRL.