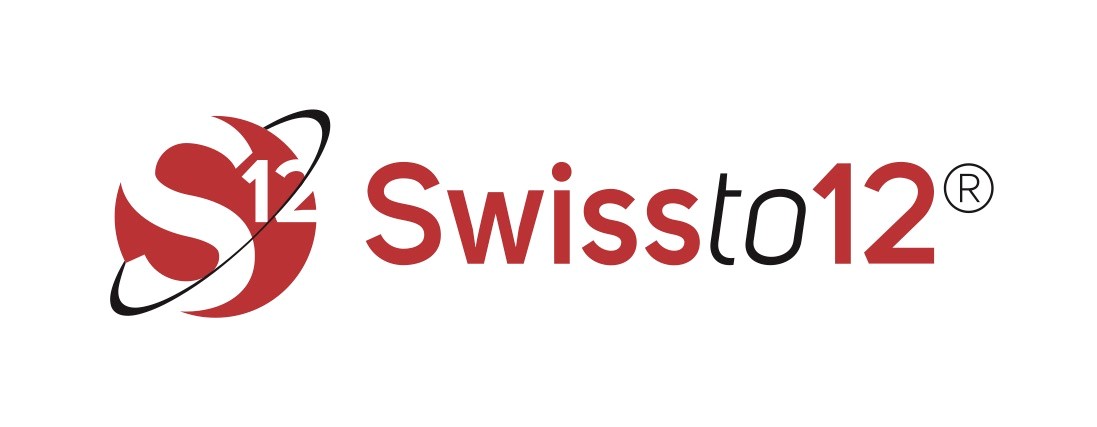
-
StatusCompleted
-
Status date2018-01-18
-
Activity Code7A.028
The objective of this project is to investigate the suitability of additive manufacturing (AM) technologies for the fabrication of RF user terminal front-ends for communications-on-the-move (COTM) applications. The first goal is to critically analyse the available AM technologies and materials and evaluate the advantages and disadvantages of each of them. In parallel, a state-of-the-art review of the current commercial COTM systems is necessary in order to compile a list of RF, mechanical, and thermal specifications for different application. This analysis allows to identify recurring critical components that can benefit from the new degrees of freedom offered by AM. A precise workplan is defined to compare the various AM technologies and materials and select the more appropriate for this type of application. Then, the selected RF components are designed by considering the flexibility and the limitations of AM. Additional test jigs for the RF measurement of the components are to be designed and manufactured together with the actual RF hardware. Finally, a few manufacturing iterations are expected to further improve the performance of the components to a satisfactory level with respect to realistic commercial specifications.
The main challenges of the project are the successful fabrication of the selected components, which essentially means: (a) their 3D-printing by stereolithography in a polymer material, (b) the post-processing steps to clean them from any remaining non-polymerized material (c) to prepare the surface of the material by chemical etching so that the subsequent metal plating has a good adhesion, (d) the electroless copper plating of the component with a sufficient thickness (depending on the skin depth) in order to become RF functional. Each of the aforementioned steps involves technological challenges that need to be very carefully controlled.
The benefits from additive manufactured RF hardware are numerous: increased design flexibility, significant mass reduction, potential cost reduction for low to medium volume production, reduced lead time (typically 4-6 weeks), possibility to replace complicated assemblies of multiple parts with a single monolithic component (or an assembly with much less parts), improved RF performance due to the possibility to implement advanced designs that are impossible to manufacture with conventional subtractive fabrication methods.
The most important feature of the components fabricated in this project is the significant mass reduction, up to 5 times compared to the respective conventional components. This mass reduction can lead to significant cost reductions, for example by avoiding heavy duty motors to point the antennas toward the satellite. The cost of the hardware itself is approximately 20% less than the conventional counterparts, while the lead time is typically between 4-6 weeks. In terms of RF performance, AM components are meeting realistic specifications established on the basis of existing commercial requirement.
In this project, different components for user terminal front-ends are developed. Some of them are part of a feed-chain, i.e. components with different functionalities (e.g. diplexers, polarizers, OMTs etc.) sitting behind the feed horn of a reflector-based antenna system. Others are parts of Direct Radiating Arrays (DRAs) which are essentially a 2D periodic repetition of a radiating element (horn, waveguide slot etc.) fed by a beamforming network. Both architectures are of interest in communications-on-the-move (COTM) applications (ground, aeronautical, maritime etc.).
The first milestone is achieved with the detailed comparison of the different AM technologies that are suitable for fabrication of user terminal front-end components. Then, the selected RF components need to be re-designed by considering the limitations of the defined AM method. The second milestone is achieved with the complete RF and mechanical design of the hardware to be manufactured. Finally, the third and last milestone is achieved with the successful fabrication and measurement of all the RF hardware and the compilation of the Final Report of the project.
Project has been completed/developed from Feasibility Study to Demo.