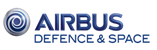
-
StatusCompleted
-
Status date2016-12-19
CAN bus is an established commercial standard, with countless literature available from the web, numerous electronic components available at low cost, and a high amount of testing equipment available from the shelf to perform rapid prototyping. As such, a CAN bus robust solution for satcom highly benefits from the commercial market efforts to streamline and ease the design of a specific CAN bus solution.
Shape the CAN to fulfil satcom requirements:
Challenge is to adapt the CAN bus protocol which has been developed by automotive industry to manage real time tasks to the constrain of the Telecom payloads management.
Integrate CAN to the platform preserving gained heritage:
The proposed solution need to build on the heritage and to cope with existing context. E3000 software and 1553B system bus management have their own capabilities that cannot be over passed.
Offer a high reliability level:
Mission availability is a key feature for telecom payload, the data bus reliability that connects several RF units must cope with that requirement by implementing redundancy and solutions to avoid failure propagation.
The solutions that exist today with all telecom primes are not fully supported by a standard. Aim of the study is to propose a solution supported by an existing standard well known and well distributed in other industries. The main objectives are
- To define in detail a CAN bus solution compatible with satcom environments and requirements,
- To insure low time to market through efficient CAN/CANopen IP availability and prepare for future enhanced industrial competitiveness based on CANopen,
To qualify CAN to enable commercial CAN bid for satcoms at study completion.
The developments defined within this project aim at enhancing the overall competitiveness and performance of E3000 satellites in order to fully answer operators’ needs and requirements. The development concerns the TM/TC architecture. A CAN bus will replace the currently used Low Speed Serial Bus (LSSB) to connect payload units and in particular the Channels Amplifiers (CAMP) to the platform.
The benefits of such evolution are:
– Less non quality issues due to CAN bus standard.
Integrated transceiver DLA are now qualified, that guarantee the electrical compatibility between nodes, with straight forward implementation needing small PC surface.
The protocol defined by Tesat, Thalès Alenia Space and Airbus DS, part of Neosat applicable documentation and also ECSS, is another key feature of CAN bus that guarantee interoperability.
– High Data rate improves payload observability allowing reducing RF performance test duration while improving the test coverage.
– CAN bus management through shared memory allow simplified operations thanks to direct access of on board software to nodes telemetries that are cyclically refreshed.
– Less harness: the physical layer is based on standard DC cable without shielding consequently without specific harness manufacturing constraints. As CAN bus use single pair per redundancy number of connection points is limited at the minimum.
SYSTEM ARCHTIECTURE
Architecture of the CAN Bus is based on a Master/Slave approach. All CAN exchanges are initiated by the CAN Bus Gateway. This approach simplifies the whole bus management and particularly time stamping aspects. As each node exchange are controlled by the CAN Bus Gateway, there is no possibility to overload the bus. The data produced by the nodes are acquired cyclically by the CAN bus Gateway and transferred on the system bus (Mil-STD 1553B). On the other way, commands received from system bus are transferred on the CAN buses by the CAN Bus gateway.
Main step of the implementation of CAN bus on E3000 is the completion of the design to move from prototype to real flight hardware standard. The qualification of the MPIU with CAN interface EQM is a critical point in order to demonstrate internally and to the end customer that hardware is ready for flight. In parallel the system team need to update the product file with all necessary documentations and tools. All these activities outcomes – MPIU EQM in one side, the complete system file (SW, TM TC database production tools, hardware and software documentation) in the other side are then tested all in one during exhaustive system test on the Avionic Test bench. It is also intended to lead in parallel activities on CAN ISO transceivers components. The following figure shows the overall development logic starting from “CAN bus for platform and payload management” activity followed by “CAN Bus Implementation on E3000” Artes 3-4 development.
A full MPIU with CAN interface EQM was built. This unit supported the unit qualification (including mechanical shocks and ESD tests) but also supported a complete end to end system test. Functional tests have been run on the Eurostar E3000 Avionic Test Bench (ATB) that provides test facilities, on board computer and software, system bus and payload interface unit (MPIU). The MPIU, part of the validation environment, embeds the modified board, implementing the CAN/LSSB IP developed in the frame of the study. CAN ISO transceiver has been evaluated: CAN ISO transceiver survey, definition of the part selection criteria, evaluation plan, risk analysis.