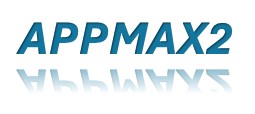
-
StatusCompleted
-
Status date2024-12-12
-
Activity Code4B.149
- Update the business plan to reflect the increased maturity of the product.
- Develop and produce B/B Models of main components to reduce the technical risks targeted in this development phase.
- Low-cost Actuator Development
- Dynamic SM
- Ball Joint B/B
- Demonstrate the functionality and performance of the components by suitable testing of the component B/B models.
- Verification of the component’s performance
- Produce a dynamic development model that is sufficiently representative of the final product to reduce the technical risk targeted in this development phase.
- Dynamic Development Model
- Demonstrate the functionality and performance of the product by suitable testing of the development model.
- Qualify a flight representative mechanism in configuration ECSS compliant and in configuration with high accuracy referencing and shock attenuation via elastomer damping.
Following key issues have been identified and handled in the frame of the project:
- Determination of key technologies to be implemented for product cost reduction.
- Determination of key needs for the customers to minimise higher level effort and higher-level cost as well as higher level risk.
- Identify solutions which allow to choose between cheap COTS parts and more expansive high reliability parts.
The mechanism provides highest robustness for on-ground handling and launch case. With the features stated here below it provides high gains for the customers for constellation and for high reliability applications.
The mechanism does not require a dedicated hold down and release mechanism. It can be remotely pre-loaded by its 2x pointing actuators to launch configuration.
The mechanism is highly pre-loaded and therefore highly robust in the launch configuration. Therefore, it can be used in the same configuration in many different applications with different requirements.
The mechanism does require an off-loading device for ground operations when a thruster is mounted not dependent of S/C orientation.
The high rel. version of the mechanism is equipped with elastomer dampers which results in very low dynamic input loads transmitted into the damping elements.
High reliability for the high rel. mechanism of 0.999999992 for deployment and 0.99999182 for in orbit operation over 2 years.
The mechanism allows later accommodation of pointing range from 15° half cone to higher angles.
Both actuators are positioned on the mechanism base frame and operated via 2x knuckle lever kinematic the mobile platform. During the launch case both knuckle lever assemblies are driven to their highest preloaded position and the mobile platform is clamped to the base frame via cup-cone release I/Fs.
There are the following Milestones in this Project:
- BB TRR
- BDR
- DM TRR
- PDR
- EQM-TRB
The work performed under this project is finished. The C-EPPM which is now called Appmax 2 been designed, the hardware has been built, fully tested and qualified.