-
StatusCompleted
-
Status date2022-01-14
-
Activity Code5C.252
The key goal and driver is to move away from classical converters and master/local references to allow a more generic approach to be facilitated across the spectrum of requirements, whilst concentrating on the overall price, mass and footprint. Using our generic telecoms processing architecture, applicable to a wide range of missions, an end-end RF system is envisaged which can be built using a small set of common building block modules. The three types of equipment developed to EQM are a set of RF equipment suitable for frequency translation (up conversion (U/C) and down conversion (D/C))
-
C / X / Ku band FSS Downconverter Equipment
-
C / X / Ku band FSS Upconverter Equipment
Realised as Master unit and Auxiliary Unit
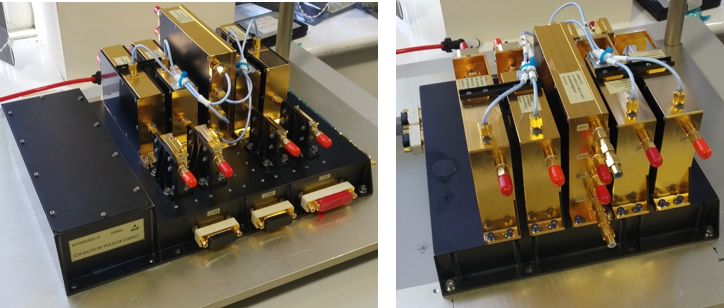
A set of MRO (Master Reference Oscillator)/ DSP Clock equipments to support not just the converters, but also the digital processor
-
MRO/DSP Clock Equipment
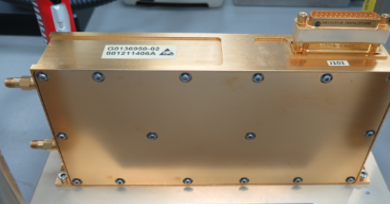
The converters need to translate the wanted carriers from the uplink frequency to the DSP interface frequency then back to the downlink frequency range. Realising a single converter design to cover C, X & Ku(FSS) with relatively minor component changes. Achieving up to 500MHz bandwidth with low noise power acceptable alias signals and minimal SWAP.
There are two variants of the DSP Clock Oscillator; 300MHz to 640MHz and 1300MHz to1500MHz.These will differ only in the VCO type and the precise PLL divider and loop filter settings. Achieving the necessary performance for clock jitter and phase noise are key challenges
When looking at the overall digitally processed sub-system, the biggest hurdle are the RF equipments needed to support the digital processor. The proposed RF solutions are aimed at addressing many of the market landscapes with the capability of covering FSS, MSS and BSS in telecoms and potentially non-telecoms missions, with the added benefits obtainable by processed missions.
To minimise the recurring cost it is necessary to reducing the number of new components and by spreading the cost of development over a number of missions. Flexibility to support a range of missions using a small number of components implies a modular design which can be manufactured in surface mount technology and can be tested automatically. The MRO/Clock is intended to support not just the converters, but also the digital processor. Wherever possible cost has been minimised by use of common components for both the converter and MRO/Clock. The OCXO: providing the frequency reference is an existing 100MHz OCXO product with Flight heritage this combined with a heritage DC-DC converter and an LC or microstrip resonator based VCO to provide the Clock signal enables a high performance competitive product.
The converter master unit comprises the following blocks
-
Master Baseplate assembly: Two-off DCDC Power Supplies, dual redundant TM/TC PCB, Power, parallel bits & Serial Bus routing
-
RF Chain (RFC) Modules: Up to 5-off RF Conversion Modules
-
Local Oscillator (LO) Module: Optional Dual Redundant Local Oscillator Module.
If no LO module is fitted, 5 RF conversion modules may be supported that would be supplied an LO from an external source. The baseplate has 2 screw-on lids that incorporate radiation shielding by being up to 3mm thick where necessary.
The auxiliary unit accommodates at least 4-off conversion modules, If no LO module is fitted, 5 RF conversion modules may be supported that would be supplied by an LO from an external source.
The DSP-Clock MRO is designed as a single I-frame aluminium lidded (with EMC gaskets) module with one side catering for DC conditioning/regulation and the other side providing RF functions. The gain stages utilise SiGe amplifiers. The OCXO is an existing 100MHz Airbus design and is also a relatively small ceramic hybrid design. Screw-in PCB assemblies provide flexibility for different payload requirements and mounted components can be updated to satisfy new or different requirements readily.
The frequency conversion equipment itself consists of up to 4 chains of RF conversion, down conversion or up conversion, along with the local oscillator generation for each chain, along with dual redundant power solution. These equipments attach to a multi-function active master baseplate providing power and optional digital TM/TC. The Master Equipment can supply up to 20 RF Modules (eg. 16 converters & 4 LO modules), with the modules distributed across 4 equipments. A smaller Auxiliary unit, without fitted DCDC converter power supplies allows the addition of several 4-pack converters per auxiliary unit.
The reasons for choosing 4 converter modules on the equipment are as follows:
-
Shared resources reduces LO & DCDC converter hardware, thereby reducing cost & mass
-
Up to 4 RF Chains share 2 LO Circuits and 2 DCDC Converters
-
Standard heritage DCDC converter can supply power to up to 4 chains plus LO circuit without modification
-
- 4 Converter Chains is a good choice for test system throughput
-
Having 4 chains per unit, configured as single converters/module makes rework and replacement of single chains straightforward
The MRO/Clock is a single box containing OCXO, VCO, PLL, Gain blocks and DC-DC Converter.
There are 2 phases Pre-Equipment’s Developments; Phase 1
-
EBB1 – Ku-UHF – RF Chain to prove the critical hybrids and filters
-
EM1 – UHF/Ku – RF Chain to prove the critical hybrids and filters*
-
EM2 – MRO – single processor clock (DSP Clock 2)
EQM Phase 2
-
EQM1 – Ku-UHF Converter equipment*
-
EQM2 – UHF-Ku Converter Equipment*
-
EQM3 – MRO – 100MHz & DSP Clock 1
The 3 EQMs will be subjected to an EQM test campaign including EMC, ESD, T-VAC and Vibration/Shock.
The plan was to undertake this development in 20 months.
COMPLETED
Airbus has successfully completed the development of all the Equipments proposed. Many of the technological advances realised in the frequency converter development are now incorporated into qualified flight Equipment’s sold to customers.
The MRO/DSP Clock Equipment is now a standard product on many payloads in orbit.