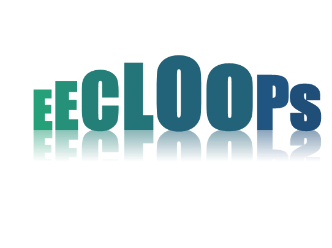
-
StatusCompleted
-
Status date2021-06-21
-
Activity Code4D.057
- Target to enhance performance of single-Phase Mechanically Pumped Fluid Loops
- Reducing pump size or speed/load by optimizing flow at the heat exchanger wall.
- Increase the TRL from 3 to 4
- Increase the heat exchanger performance, with a target of a factor of 4 or more per unit area
An electrohydrodynamically (EHD) enhanced cooling loop heat exchanger breadboard model was designed, manufactured and tested integrated with and externally pumped fluid loop and related Ground Support Equipment Test-Bed.
The main challenge in this project was the development towards a cost-efficient product, while improving performance of existing cooling loops.
Technically, this needed to be translated into materials and manufacturing methods that do not compromise the performance or cost in later stages of development of this new type of new heat exchanger, while implementing redundancy and meeting 3 W/K thermal coupling for 35W/cm2.
Due to the enhanced performance of this heat exchanger the mechanical pump size as well as the overall system size, weight and power could be reduced. Ground testing consistent with in-orbit operation.
- Compatible with a bus voltage of 50 and 100 VDC
- >15 years lifetime
- Scalable to handle up to 10kW heat transfer power
- Redundant fluidic paths
- Simple mechanical and fluidic interfaces
- 50% reduction in delta temperature in “ON”
- 0.3 W power consumption
This heat exchanger will be located in the mechanically pumped fluid loop in close connection to high power hotspots. It consists of fluidic interfaces to the fluidic loop, screwed interface to the load and flying leads. The casing includes the EHD components within internal flow path.
The development work was divided in 4 major work packages:
- Requirements & Feasibility
- Breadboard heat exchanger design
- Manufacturing, test and verification
- System performance analysis & trade-off
The milestones were Design Review, Test Readiness Review and Final Review
The project is finalized and has successfully collected a complete technical specification based on requirements from satellite primes, built and verified a BBM reaching TRL4, with performance mapped in a parameter space covering several applications. Areas for improvement are identified and a plan for reaching TRL 5/6 within 18 months is defined.