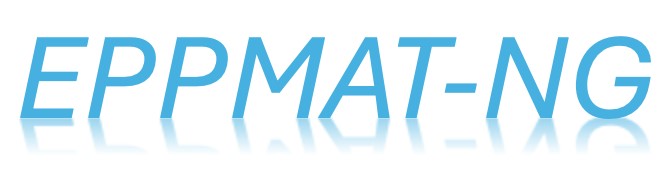
-
StatusCompleted
-
Status date2024-06-11
-
Activity Code4B.154
Geared actuators are the key elements in all kinds of pointing mechanisms used in space applications. The actuators are providing the desired motion and are often directly in the structural load path. Further, the stepper motors dissipate heat which needs to be controlled to avoid overheating of the stepper motor windings and keep the actuator in the allowed temperatures when not powered. These challenging boundaries often result in complex design solutions, leading to high costs and labour effort.
Therefore, the overall objective was the development of a geared actuator at lowest possible cost (manufacturing parts and labour effort) by maintaining full ECSS compliance and performance of BGA´s actuator SA15.
Following key issues have been identified and handled in the frame of the project:
- Simplification of manufacturing parts.
- Simplification of assembly process.
- Keep the part-count as low as possible.
- Use identical parts as often as possible (e.g. assembly “Small PG Stage 1” is used two times within the gear assembly – as stage 1 and as stage 2).
- Use standard parts (bolts, shims, etc.) as often as possible and avoid custom solutions.
- All bullets above have one goal: minimise the costs of the actuator.
- Keeping the mass as low as possible.
The performed work on the LA15, within the ARTES programme, has been very important to be in the position to offer APPMAX2 and APPMAX3 mechanism (BGA´s 2-axis and 3-axis pointing mechanism) to customers at an attractive price.
The design was developed to a state that enabled immediate manufacturing and successful testing.
The developed LA15 shall has the following key characteristics:
- Delivered Output Torque: 15Nm at the gear’s output shaft, considering ECSS motorisation rules.
- Unpowered Detent Torque (purely magnetic contribution): 13.05Nm at the gear’s output shaft (already considering an ECSS uncertainty factor of 1.1).
- Step Size: 0,00838deg.
- Total Backlash:
- less than +/-0.6deg (standard backlash gear).
- less than +/-0.1deg (low-backlash gear).
- Nominal Step Rate: 20Hz.
- Dynamic Loads: 90g / 30gRMS (qualification).
- Mass: approx. 1490g.
- Temperature Range:
- Maximum Operational Temperature Range: -40°C to +120°C.
- Maximum Non-Operational Temperature Range: -100°C to +130°C.
- Winding Temperature (operational) up to 130°C.
The LA15 consists of a hybrid stepper motor (which was developed in the frame of another (EPJT) ESA project), a small PG gear set which is followed by an output (large) planetary gear (LPG) stage and high load main ball bearings. The LA15 can be equipped with different windings allowing fine tuning of the delivered output torque.
The only milestones are a Trade-Off Review (TOR), a Preliminary Design Review (PDR) and the Final Review (FR). All meetings have been successfully held.
The work performed under this project is finished. The LA15 has been designed, the hardware has been built and fully tested.