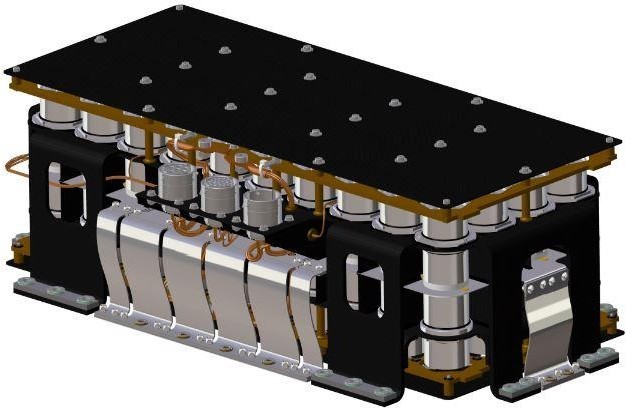
-
StatusCompleted
-
Status date2021-01-08
-
Activity Code4A.055
The aim of this project was mainly to reduce the mass of the packaging of an already existing typology of battery while implementing an individual cell replacement feature. The mass improvement will increase as well specific energy of the battery making it also interesting for GEO missions. The individual cell replacement feature will be mainly useful if an issue occurs on the battery during spacecraft MAIV/T activities. This allow to just replace one or multiple cells affected by the issue instead to the whole battery.
Main challenges of this project were to reduce the structural mass of the battery packaging by more than 50% while introducing a new feature of individual cell replacement.
Main benefits of the product with respect to competitor comparative products are a higher energy density of the battery and the possibility to replace Lithium-Ion cells individually in case of issue during the MAIVT of the battery or of the spacecraft.
The product has three main features which are a stiff and lightweight structure made of CFRP, an efficient heatsink made of aluminium and an innovative cell clamping system allowing cells replacement.
System architecture is to replace actual battery packaging made of aluminium by a CFRP structure which have a dedicated thermal heatsink for cell thermal dissipation. The cell clamping system developed allows as well individual cell replacement
The project started with a state of the art and a material & process trade-off. The packaging factor and mass breakdown of several batteries was analysed. After choosing the materials and processes, the optimisation and sizing of the packaging was performed wrt thermal and mechanical loads. An EM was then manufactured and tested and compared to the prediction (correlation) and to the existing packaging.
Project has been completed.
The resulting manufactured Engineering Model (EM) battery showed a mass recovery of almost 2kg with respect to the corresponding battery. The target of 1.3 for the packaging factor was almost achieved with a value of 1.327.
Battery test results showed good thermal and electrical performance as expected in the simulation and similar to those of the comparative battery. Mechanical tests were unsuccessful and stopped after Random Z load because of glue detachment between the CFRP core and the thermal middle plate. This non-conformance occurred during thermal cycling but it is more linked to the gluing process and surface preparation than the thermo-elastic loads.
Almatech is nevertheless confident that both mechanical performance and packaging factor target can be achieved in further project steps by especially mastering the bonding process between interfaces and by modifying slightly the thermo-mechanical design.