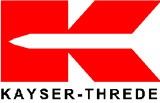
-
StatusCompleted
-
Status date2010-09-20
-
Activity Code4E.008
Big telecommunication satellites have extensive requirements for sensing during nominal operation and testing:
- Temperature sensors for thermal control and monitoring (up to 500 on board temperature sensors),
- Load monitoring during qualification and verification testing,
- Voltage, current and power monitoring for housekeeping,
- Pressure and temperature measurements for the propulsion system control,
- Positions and contact sensors for S/C configuration.
Further instrumentation of interest for optimized satellite verification (e.g. in flight) and operation if feasible w/o major budget and cost impacts are:
- Mechanical and thermal loads of structures (prime structure, solar array, reflector),
- Propellant fill level sensor,
- Sun position.
Current sensing technologies do not allow a high degree of multiplexing which results particularly into a cumbersome harness (e.g. 150 temperature sensors x 2 wires = 300 wires). Fiber optic sensing (FOS) has a range of advantages in comparison to conventional sensors, especially under severe environment conditions such as space applications. Moreover, the following features of fiber optic sensors recommend their application in innovative technical fields, e.g., for integrity and health monitoring of telecommunication satellites, where the equivalent electrically based measurements can not be performed or only with low performance characteristics:
- Complementary instrumentation for temperature, strain, pressure, etc.. sensing,
- High degree of multiplexing and multi-parameter design (hundreds of sensors),
- Small cross dimension, lightness, very low heat conduction,
- Long-term stability at operation in hostile environments (EMI, high temperatures),
- Remote, electrically passive sensors, ideal galvanic separation,
- Ability for embedding in structures, implementation as a "nervous system",
- Capability for distributed sensing by passive multiplexing of sensors along a single fiber,
- Low system mass.
In the course of this activity, the potentials and benefits of fiber optic sensing technologies shall be demonstrated by a reasonable combination of analysis and testing. A demonstrator which is composed of satellite mockups, instrumented with fiber optic sensor, fiber optic harness and signal processing shall be built and tested.
The following key issues will be addressed:
- Identification of FO sensing applications for satellite system improvement taking into account the entire life cycle of the satellite,
- Assessment of technical maturity of existing FOS solutions,
- Development of representative satellite mock-up with integrated FO sensing systems,
- Development of a high multi-plexable and multi-tasking signal processing unit capable to readout >100 sensors,
- Representative testing of the demonstrator including vibration and thermal-vacuum testing for selected satellite mock-ups,
- Cost-value assessment.
Fiber optic sensing (FOS) technologies possess the potential to replace a variety of existing sensing solutions in telecommunication satellites, e.g. temperature sensors for temperature control. Furthermore, the potentials of FOS allow the implementation of new instrumentation functions. In the following some examples are listed for improved functions (means replacement of existing solutions) or new functions:
Improved functions
- Reduced harness, lower mass, easier assembly,
- Feasibility of a higher level of redundancy,
- Non-intrusive monitoring, e.g. for reflectors (sensor + harness have no impact on the structural function),
- Usage of FOS for the entire component life cycle (= usage of FOS for manufacturing, testing/verification, operation and advisory),
- Improved satellite operation with higher number of sensors (thermal control, antenna and solar array positioning, etc).
New functions
- Combination of sensing with telecommunication functions (e.g. internal data link),
- Embedded sensors (e.g. in prime structure, solar array and reflector) for easier integration/assembly,
- New measurands, e.g. propellant fill level sensor,
- Thermal flow or temperature profile monitoring.
The activity is divided into two main parts. The first task "Definition of Satellite Monitoring Requirements" is covering all activities related to the definition of the monitoring requirements and the subsequent selection of FOS applications in a standard GEO telecommunication satellite.
The FOS technology shall be traded against existing sensing solutions to clearly identify the potentials of fiber optic sensing for replacing existing sensing concepts or for new instrumentation with regard to the monitoring requirements.
Based on the technical potentials of FOS, satellite specialist (Astrium) + payload supplier (Tesat) + structure specialist (HPS) shall derive candidate applications which have so far not been considered due to limitations of existing solutions.
Phase II is divided into an analysis phase and design / hardware oriented phase. After the execution of all design analyses with regards to to the measurement requirements (multi-parameter, multiplexing, etc) the demonstrator design shall be derived.
The project started in September 06 and is currently in the detailed design phase. In phase 1, the generic monitoring requirements for satellite instrumentation have been defined taking into account the entire life cycle of the satellite system, subsystem and components. The term generic in this context means that the definition of monitoring requirement should not have been influenced by constraints such as mass, costs or technical impediments. The outcome of the monitoring requirements has than be compared assessed with regard to the technical features and potentials of fiber optic sensing. Based on the available technical maturity of fiber optic sensing the following applications have been selected for demonstration testing:
- Smart Panel demonstrator: Representative for a standard panel with embedded FO temperature sensors for thermal mapping for thermal control. Via FO sensing a high amount of temperature sensors can be embedded into panels during panel production. Thermal control can be improved and labor hours for harness assembly by reduced,
- Reflector demonstrator: Due to the lack of low mass, non-intrusive sensors, the behavior of reflectors in space is not well understood. Via the in-orbit demonstration, important design data for performance characterization is feasible,
- Tank demonstrator: FO sensors have potentials for tank fill level measurements and pressure sensing of satellite tanks.