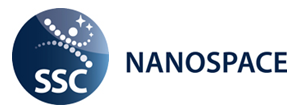
-
StatusOngoing
-
Status date2017-04-12
-
Activity Code4B.085
The aim of the project is to assess the applicable passivation requirements and to develop a breadboard model of a Gas Passivation Valve (GPV) suitable for European geostationary telecoms platforms. In addition, the project tasks include the development of a detailed design, development and verification plan for further development towards a GPV product. The GPV design permits the release of all stored energy in the form of pressurant gas during the spacecraft disposal phase. Design demands at the valve level must be sufficient to fulfil the system level passivation reliability and mission success criteria without releasing additional space debris during operation.
The major challenge of the GPV development is to maintain a very low leak rate throughout the required life time of more than 21.5 years (18 years in space and up to 3.5 years before launch). In addition, the valve actuator must be reliable when subjected the required pressure and temperature environments throughout the operational life time.
The GPV has the benefit of being small, lightweight, has simple interfaces to the satellite and its actuation does not include significant shock. In addition, it is possible to test the GPV for leakage and the status of its actuation mechanism before and after final assembly.
By including MEMS technology in the assembly, it is possible to achieve a GPV with very low mass while maintaining conventional electrical and mechanical interfaces. The GPV consists of two major features: The sealing assembly, which ensures leak tightness; The actuator, which ensure that the opening of the seal on activation command. In contrast to pyro valves the GPV actuator is inherently shock free.
The GPV design allows installation either on the high-pressure or low-pressure side of the propulsion system. Installation on the high-pressure side will imply minimum impact and no dependability on other components (such as the pressure regulator) in existing systems.
Installation on the low pressure side will have to take into consideration a functional and leak tight regulator until passivation. The GPV is designed for the worst case scenario, which is installed upstream the regulator.
This project is organised into the following tasks:
- Evaluation of the system level requirements, definition of the project outline for the sub-system, and identification the equipment requirements to fulfil the passivation requirements
- Identification of the available suitable building blocks within Europe as well as of additional elements to be developed to fulfil the requirements
- Production and test of breadboard model(s) of critical components
- Evaluation of the design, functional and performance requirements.
Following the project initiation in March 13th 2015 the GPV requirements, system schematics and operation strategy was formed in collaboration with European telecommunication satellite primes and operators. The valve sealing assembly and actuator was developed and the valve functionality was tested against critical requirements regarding sealing and high pressure actuation. The valve show very low leakage, high mechanical strength and repeatable actuation. The project is finalized with a development plan for further developments towards flight qualification. The project and its results were presented at ARTES presentation days 07/03/2017.