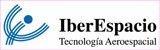
-
StatusCompleted
-
Status date2012-12-05
The potential increase in the operational and non-operational temperature limit for spacecraft electronics in the near future is demanding heat transfer devices which are able to operate up to 125º C.
An increase in the operating temperature of the heat transport systems provides the means for an optimization of the thermal control systems on board, with reduced radiator areas.
In this line, IberEspacio, Thales Alenia Space and EADS-CASA Espacio have performed an extensive and comprehensive set of activities to develop a High Temperature Loop Heat Pipe & Radiator. The HTLHP activities started with the discussion of the HTLHP concept to the analysis of the test results and qualification program definition with the objective of the development and full characterization of a Loop Heat Pipe (LHP) and radiator able to efficiently operate at temperatures up to 125º C. That implies that the developed technology acquires a technological readiness level at least TRL 5, prior to qualification.
Main challenges of HTLHP project are the development of:
- LHP able to efficiently operate at temperatures up to 125º C and to transport at least 500 W. The LHP shall be compliant to a lifetime of 15 years without degradation. Thus, the Non Condensable Gas (NCG) generation related to the compatibility of the LHP working fluid and materials will be the driver of the design,
- Long-size high thermal conductance evaporator (length of the evaporator > 400 mm),
- Condenser with parallel branches,
- High thermally conductive CFRP radiator and optimization of its interface with the LHP condenser.
The use of LHPs as heat transport systems imply the following advantages:
- LHPs are passive devices; no external power supply is needed,
- Efficient thermal link between the equipment and the radiator (high thermal conductance),
- High heat transport capability, linked to the use of an optimized capillary pump,
- Delocalization of the radiator,
- Easy integration, linked to the transport lines flexibility,
- Operation in different orientations, including adverse elevation (condenser below the evaporator), particularly significant for ground testing activities,
- High reliability.
In addition, the development of a HTLHP and Radiator, taking into account the expected increase of the operational and non operational upper temperature limit for spacecraft electronics, implies the following additional advantages:
- Radiators with reduced areas, linked to the increase of the LHP operating temperature. That is related to:
- Mass optimization,
- Easier integration.
- Increased thermal conductance, linked to the parallel condenser and large evaporator,
- Enhanced interface between the equipment and the LHP, linked to the large evaporator,
- Enhanced interface between the LHP condenser and the radiator, linked to the development of a high conductive radiator with embedded condenser tubing.
In the HTLHP project a system including the following elements has been developed:
- LHP consisting of:
- Evaporator, large size, consisting of:
- Stainless Steel (SS) compensation chamber,
- SS evaporator case,
- SS primary wick, Outer Diameter (OD) = 22 mm,
- SS secondary wick,
- Aluminium evaporator saddle, saddle footprint of 400 mm x 100 mm.
- Titanium vapour line, 3 m length, 6.35 mm OD,
- Titanium liquid line, 3 m length, 6.35 mm OD,
- Bimetallic connections between the SS evaporator and titanium transport lines,
- Titanium condenser line with two branches in parallel, embedded in the radiator, 4.5 m length, 6.35 mm OD,
- Capillary blocker, located at the condenser outlet, to prevent the vapour flow from one of the condenser’s branches to the other and to the liquid line,
- Ammonia as the working fluid.
- Evaporator, large size, consisting of:
- High temperature Carbon Fibre Reinforced Plastic (CFRP) radiator with an area of 700 mm x 700 mm, consisting of:
- CFRP skins,
- Aluminium honeycomb core,
- Graphite foam for the interface between the radiator and the condenser tubing.
Step 1: The activity started with the specifications consolidation and existing technologies and patents review to define the HTLHP concept. Then, a comprehensive trade-off and testing of dedicated breadboards were carried out to select the HTLHP prototype approach.
Step 2: The HTLHP prototypes were designed and manufactured. A Thermo Mathematical Model (TMM) was built-up to predict the LHP performance. The test plan, set-up and procedures were prepared.
Step 3: The test campaign was performed, including different environments and orientations. After a successful test campaign and TMM correlation, a Qualification Program was defined as the next stage in the HTLHP activity.
The ARTES 5 HTLHP Project is successfully finished. The technologies and hardware developed in the frame of the project:
- ammonia HTLHP with SS wick and Ti lines (IberEspacio) and
- high thermally conductive CFRP radiator (EADS-CASA Espacio)
are fully compliant with the specification elaborated and consolidated by Thales Alenia Space. Important technology achievements have been obtained during the course of the HTLHP development:
- Long-size high thermal conductance evaporator,
- Novel application of IberEspacio-developed stainless steel wick,
- Use of ammonia for 100-125º C saturation temperature,
- Capillary blockers for parallel branches condenser,
- Embedded titanium condenser in high thermally conductive CFRP panel.
The objectives of the project have been fulfilled and as a consequence it is possible to propose advanced and solid technology to meet new challenges in the spacecraft thermal control field.