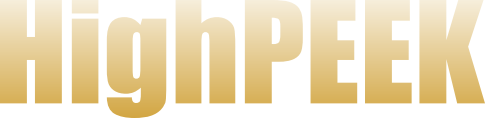
-
StatusCompleted
-
Status date2023-01-23
-
Activity Code4A.078
The project objectives are to replace metallic telecom satellite secondary structure parts with conductive thermoplastic ones. Mass saving of at least 50% and lead time reductions are aimed for. The parts need to withstand the GEO space environment, with launch loads and vibrations, outgassing and UV resilience being important requirements.
Two part families are considered in detail: 1. enclosures and 2. support structure and brackets. Real metallic parts used in spacecraft were selected as baselines which to replicate into a thermoplastic versions.
The parts should also have conductive properties. Two approaches are used: material conductance and as well as atomic layer deposition (ALD). The first enables lower-level conductance through the material itself, enabling application such as electrostatic discharge. For this the consortium developed its own conductive PEEK material with optimal properties for the task at hand.
The latter is a method developed by the consortium, wherein nanoscale coatings are very conformally coated over a thermoplastic part. The coating can be very conductive, opening up low – resistance applications, and can be selectively coated with the selective use of thermoplastics.
Example application 1: Microwave power metallic relay (left) and equivalent re-designed, significantly lighter thermoplastic version (right)
Example application 2: On-Board Computer metallic housing (left) and re-designed equivalent thermoplastic version (right)
Example application 3: conformally coated conductive 3D-printed part (left) and a 3D-printed UV-sensor cirtcuit next to its original (right)
Main challenges include verifying that the part can withstand long time periods in a GEO space environment, particularly regarding UV. Additively manufactured parts need to also be checked regarding the isotropy of their mechanical properties.
The replicated thermoplastic versions were measured and compared with the baselines, with the thermoplastic ones being at best 63% lighter while still retaining good enough mechanical properties to withstand launch loads and vibrations.
In addition, the thermoplastic parts can be manufactured using additive manufacturing, enabling fast lead times and flexibility in design geometry. If for example a modification was necessary, it could be done within days.
An ALD coating on top of the thermoplastic part is able to conduct with very low resistance, and with thick enough coating this can brought down to baseline resistance of the coating material. In addition, the ALD coating can significantly decrease thermoplastic outgassing. The coating combined with 3D-printing can also be selectively coated, enabling novel applications such as complex, three-dimensional circuitry.
The thermoplastic parts are able to replace a secondary structure metallic part without increasing the risk of mechanical failure. They are able to safely discharge electrostatic build-up, and with ALD coating achieve low-resistance applications. The chosen thermoplastics have low inherent outgassing (such as PEEK) and with an ALD coating this can be decreased significantly still.
Complex geometry parts will be prototyped and manufactured faster and cheaper.
The 3D-circuit can be integrated into a larger printed part and so gain more mass savings and volume optimization.
N/A
The project has three main phases – secondary structure family review and part selection, first test part and conductive thermoplastic manufacture and test, and then based on the results, optimization and verification tests on the optimized parts.
The project selected the part families and parts themselves (almost all are from existing space missions or other ARTES projects) and thermoplastic versions have been manufactured. Two iterations of the selected parts were printed and extensively tested.
The consortium produced its own conductive PEEK compound with improved thermal and outgassing properties.
Selective coating using ALD has been shown to work and selectively coated test pieces have been successfully produced. Two circuit demos were built, of which one operated a reprogrammable microcontroller and a LED while the second a UV-sensor.