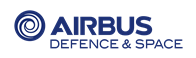
-
StatusCompleted
-
Status date2015-11-16
-
Activity Code4D.034
The overall objective of the ARTES 5.2 activity was to establish TRL 5 for a HiPeR flexible film radiator based on the technology described above.
In particular, the activity was performed in two phases:
1 A bread board programme was aimed at establishing material properties after exposure to environmental conditions. In particular radiation exposure tests were performed during this phase on flight-standard coupons according to qualification levels.
2 A confidence test programme on a representative Engineering Model was aimed at establishing TRL 5. Focus was on mechanical (acoustic) and thermal tests.
SYSTEM ARCHITECTURE
As an illustration of the above, consider an example application where a “stood-off” radiator is needed which is required to be mounted on an existing S/C wall. Such applications occur frequently in science and/or EO missions where components require large dedicated radiator panels mounted on the S/C structure (e.g. the 2m2 ALADIN radiator on the Aeolus spacecraft or the 1.5m2 SORA radiators on the Solar Orbiter spacecraft). The HiPeR flexible film radiator system architecture is shown below in comparison to a conventional solution based on an aluminium sandwich panel. Clearly, the replacement of a relatively heavy aluminium sandwich panel by an equally- or better thermally conductive lightweight film offers a mass-benefit. In addition, the mounting of such a flexible film radiator is significantly simplified applying “MLI-like” standoffs in contrast to the heavy isostatic mounts required for a rigid panel.
The key issues which the ARTES 5.2 programme has addressed were the following:
- Compatibility of the technology with the space environment, in particular radiation
- Thermal Performance of the HiPeR concept.
- Mechanical performance the HiPeR concept during launch loads (sine, random, acoustic).
HiPeR flexible film radiator performance was evaluated in the example case of an 5m2 East-/ West radiator panel mounted on a S/C closure panel. In this specific case, heat is assumed to be transported to the radiator by a LHP or similar system.
- Use of new enabling high performance materials / components
- 365 W/m^2 (for +50°C radiator root)
- i.e. ~10% improved thermal performance per m2 compared to state-of-the-art Al radiator system
- Low Mass/simple design: Flexible Radiator, compare to MLI
- 10.8 kg/kW
- i.e. ~50% mass reduction
- Inexpensive: Low (non) recurring cost and minimal AIT activities
- ~50% recurring cost reduction (actual cost performance is proprietary)
In addition there are some additional benefits which are less easily quantified e.g.:
- Scalability & Modularity
- HiPeR elements can be combined, or in parts used as self-standing components in thermal systems. Accommodates all heat transport technologies; heat pipes, LHP, MPFL.
- Low risk implementation for system primes
- Simplicity of design. Low risk application.
- Easy customisation to mission spec.
- Offers more design flexibility in satellite architecture or late modifications (trim-ability)
- Easy and late integration capability
The proposed product was a flexible film radiator panel.
Employed in the radiator is a proprietary laminate of lightweight, low cost flexible films with optimized thermal properties. The laminate is a highly flexible yet robust sheet of material with an in-plane thermal conductivity between 4-10x higher and a mass 2x lower than an aluminium sheet of the same thickness.
The resulting flexible laminate may be fixed to an MLI blanket and/or a supporting structure using standard methods such as stitches, velcro’s, clipwashers, standoffs, grommets, etc.
Attached to- or embedded in the laminate are condenser tubes (e.g. for a constant conductance heat pipe or LHP).
The activity was kicked off at ESTEC premises on 17-09-2014.
Work until the BDR on 01-10-2014 focused on establishing a requirements baseline in collaboration with the end-user Airbus DS Toulouse and on the conceptual design of a HiPeR flexible film radiator.
From October to the MTR on 05-12-2014, work focused on performing breadboard tests and establishing the detailed design for the HiPeR Engineering Model EM-1.
After the EM-1 TRR on 09-04-2015, testing was performed including thermal balance testing, thermal cycling and acoustic noise testing.
The final project results will be presented at the Final Review.
All project activities with exception of the Final Review (scheduled mid-September 2015) have currently been completed.
HiPeR has been shown to survive Sine-, Random and Acoustic noise environments corresponding to launch and the thermal- and radiation environment corresponding to 18 years in GEO orbit.
During TB testing it was found that thermal performance is above the predicted performance, validating the thermal design.
Also the market assessment and cost model for HiPeR radiators were updated taking into account the latest insights, confirming the validity of the business case and resulting in a follow-on proposal for ARTES 34 development.