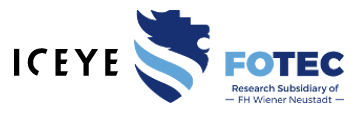
-
StatusCompleted
-
Status date2020-11-09
-
Activity Code4B.132
There are two primary objectives for project ICEYE:
- The use of the FEEP (field emission electric propulsion) ion thruster technology for propulsion. This allows high efficiency in terms of propellant use and superior controllability from the sub-µN range up to the mN range.
- The PPU for operating the thruster is based on COTS components and was specifically tailored to the needs of a FEEP propulsion system. The in-orbit test is used to verify its functionality.
The following secondary objective for project ICEYE is:
- The housing for the seven IFM nano modules is made of aluminum with the additive layer manufacturing process combined with CNC machining and surface treatments. This mission will also prove the usability of ALM manufactures for space applications.
Apart from the ion emitter itself, the module including housing, reservoir, heater and electrodes needs to be miniaturised. This is particularly challenging since a high voltage of up to -10 kV / +10 kV is being used.
The PPU being able to generate high voltage for emitter and extractor, drive the heater and neutralisers, and measuring the reservoir contactless, has been developed from scratch with COTS components only.
Compared to existing ion sources, the large amount of propellant (up to 250g) presents a challenge in terms of heating, surface tension and spilling.
The IFM Nano Thruster addresses the urgent need of a propulsion system for micro- and nano-satellites: its wide range of thrust (1μN to 1mN), the excellent throttability, and a high specific impulse (Isp up to 5000 s), allow to significantly increase the mission range of such satellites. The high Isp on the other hand allows for very high delta-v manoeuvres at a high propellant mass utilisation efficiency (80%). The modularity and the small volume (less than 1 dm³ including propellant and electronics) and its light mass (0.8 kg), make the thruster suitable for all small satellites from 1 to 500 kg.
There are major components of the cluster which are essential for proper operation:
- The housing is made out of aluminium and manufactured as one part using ALM process. This is a novel approach and vibrational tests have not shown any issues.
- The cluster uses seven individual IFM nano thruster modules. These have undergone several test and qualification procedures.
The cluster for project ICEYE consists of seven individual and individually controllable IFM nano thruster modules embedded into a common housing.
A common power bus is shared between the seven individual modules but mechanical relays can selectively remove modules therefrom. Two RS-485 communication busses are implemented (one branch with three, another with four modules attached to) which allow communication with the OBC.
The RS-485 transceivers are rad-hard and guarantee unblocking the bus once the supply voltage is removed. This allows the OBC to decide which IFM nano thrusters shall be active.
The project started after the PDR. Before that, prior work was performed to estimate the major risks of the project. All work before kick-off has been reviewed in a PWR. After the design of the housing and the mechanical and thermal simulation, a CDR was successfully completed. Then the thrusters and the housing were manufactured. The performance of the IFM nano thruster modules were determined individually. After integration into the common housing and a successful operation of the entire cluster, the Flight-Readiness Review was completed. In-orbit commissioning of the thrusters was successful and the thrusters are now operating as intended.
The project is now complete and the in-orbit experience has helped to substantially boost further sales of the IFM nano thrusters. This project was supported under an ARTES Competitiveness & Growth – Demonstration Phase – Atlas project.