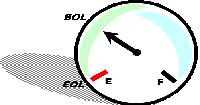
-
StatusCompleted
-
Status date2015-01-12
The overall goal of the project was to design and manufacture an engineering model of a volume gauging system and experimentally verify the novel gas injection concept with it. This included the following major steps:
- to identify the market requirements and based on that establish a subsystem design,
- to develop the critical components using MEMS technology, and
- to design, build, and test an engineering model of the gauging system for demonstration
The three major drivers for the gauging system have been performance, miniaturisation and integration.
A designed, manufactured and tested propellant gauging system models based on a novel and patented gas injection principle. No systematic variation detected with changed amount of injected gas
The mathematical model and thermodynamic model has been verified with experiments and all experimental results are in agreement with our EcosimPro model!
The work has demonstrated that a propellant gauging system can be realized such that accuracy better than +/- 3 litres of propellant in an 800 liter tank can be achieved.
The system design also enables improved accuracy with multiple injections, pressure balancing capabilities and the possible to passivate satellite tanks at EOL.
A full volume gauging system consists (as a minimum) of the following major components; an inlet filter, a sample volume tank (SVT), a latch valve, a normally closed flow control valve, two absolute pressure sensors, a differential pressure sensor, and at least one check valve.
The project was finished in November 2014.
Project closed.