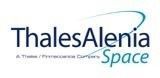
-
StatusCompleted
-
Status date2014-02-27
-
Activity Code5B.064
The main objectives of the activity are:
- Research and trade-off antenna reflector moulding techniques and tooling methods that could be applied with the aim of reducing cost and lead time.
- Characterise the selected materials of the mould within the temperature and pressure range of interest.
- Develop the selected tooling method and provide a mould for the manufacture of an Engineering Model of a Ku-band antenna reflector.
- Carry out the reflector EM manufacturing and testing, comprising thermal cycling with thermal distortion measurement and mechanical loading.
A comparison of the performances of the two reflectors (one manufactured with standard technology, the second manufactured with new technology) gave the possibility to evaluate the new mould
- Similar accuracies can be achieved with traditional and cheaper graphite,
- Similar thermal stabilities can be achieved with two mould technologies,
- The strength of the design is not affected by usage of a different graphite for mould,
- Cost saving.
The extreme accuracy requested for Ku Band mission lead to a technology employing low CTE materials, tipically isostatic graphite.
Extruded graphite has properties that are similar to isostatic graphite, but with a lower cost of basic material. The coarse graphite as the best choice for achieving high performances reflector even using a cheaper material for mould. In this respect it represents the best rate between cost and quality as far as the main characteristics of graphite mould are still maintained (low CTE, stability, strength, machinability etc) even in presence of a drastic cost reduction.
From a cost point of view, based on experience the cost of a graphite mould is as follows:
- From 40 up to 50 % for base material,
- From 40 up to 50 % for machining and checking, being the superior limit applicable for highly shaped surfaces,
- A residual 10 % for bonding & sealing, shipping and so on.
The percentage of the cost related to mould manufacturing phases doesn’t vary, while up to 50 % of the actual cost can be drastically reduced, up to 50%.
A first step of activities consisted of the description of the actual status of mould technology and reflector manufacturing technology.
An antenna manufactured using traditional technologies was selected to be a reference for performances comparison.
An exhaustive state-of-the-art study concerning the moulding technology was prepared to provide a panoramic view of possible technologies.
A specification for mould procurement was prepared.
The design phase went through preliminary and refined analyses up to the delivery of mould manufacturing documentation.
The mould was manufactured and tested
The new mould technology can be used for reflector manufacturing provided that care is used for release agent selection and application.