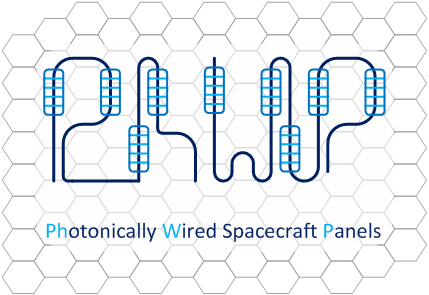
-
StatusCompleted
-
Status date2018-01-19
-
Activity Code4A.043
Fiber-optical sensors are used in many fields but are currently not yet established in spacecraft. PhWP aims to examine the use of them in spacecraft panels.
The project evaluates in detail
- AIT effort,
- mass impact,
- power impact,
- reliability and FDIR capability,
- EMC/EMI,
- costs and
- possible applications
of FOS and compares the properties with the ones of commonly used electrical sensors.
Following this, a photonically wired spacecraft panel breadboard is designed and tested.
Fiber-optical sensors (FOS) reacts with wavelength shifts at inscribed Fiber Bragg Gratings (FBG) when suspended to temperature changes and strain. In order to use FOS for temperature housekeeping in spacecraft the FBG has to be decoupled from the surface since otherwise it is not possible to differentiate between a change in strain or in temperature.
Another challenge which needs to be faced is redundancy. PhWP aims to demonstrate fiber-optical sensor buses which also serve as means to transmit data. In case of fiber breaks at any point, the functionality of parts or all sensors and the data transmission is noto given anymore, which significantly reduces the reliability and endangers the mission. Reliability concepts when using bus networks need to be established and tested.
FOS provide several benefits compared to their electrical equivalents:
- Decreased AIT effort: while electrical sensors are wired point-to-point, FOS can be established in a bus topology with multiple sensors in one fiber resulting in a significant effort reduction during integration.
- Decreased mass: due to the bus topology of PhWP the number of used wires and connectors is reduced resulting in a lower mass.
- Decreased cost: PhWP aims to reduce the number of sensor lines using FOS bus networks resulting in a less complex and less expensive integration process.
- Increased EMI resistance: due to their physical properties optical-fibers are completely unaffected by EMI in contrast to electrical sensors. In addition, FOS is no source for EMI
- Increased bandwidth: optical-fibers can be used to transmit data with very high baud rates in parallel to use them for housekeeping monitoring.
PhWP’s main feature is the fiber-optical sensor network directly embedded in spacecraft panels. PhWP shall demonstrate the benefit of the properties of FOS as low mass, EMI resistance with providing a wide bandwidth for data transmission.
The embedded FBGs make sure each sensor reflect a different wavelength, guarantying unambiguous measurement values and allows to establish a bus network.
PhWP also features an FBG transducer design which combines an optimized thermal conductivity with decoupling strain from the structure to allow a stress-independent measurement of the temperature.
Using one CFRP panel and two aluminum panels with a honeycomb core to embed the FOS network shall demonstrate the flexibility and interconnectivity of optical fibers implementations in spacecraft.
PhWP consists of three individual panels arranged in a 90° setup as show in the figure below.
The panels have the size of 90 x 90 cm and 30 x 30 cm respectively. The fiber-optical network featuring fibers for housekeeping measurements and data transmission are embedded in the panels and accessible via fiber-optical connectors for the interrogation and interconnectivity between the panels.
The PhWP project is subdivided in two steps with the goal to establish a techno-economical assessment of photonically wired spacecraft panels. In the first step a review of the photonic technology is to be carried out in parallel to survey the state-of-the-art satellite platforms w.r.t. AIT and mass parameters for housekeeping. After an architecture definition and the selection of the key components the breadboard shall be designed as initialization of step 2. The manufactured breadboard shall finally be mechanically tested in order to demonstrate the feasibility of embedding fiber-optical networks in spacecraft panels. A technology roadmap closes the project.
The project has been completed in October 2017.