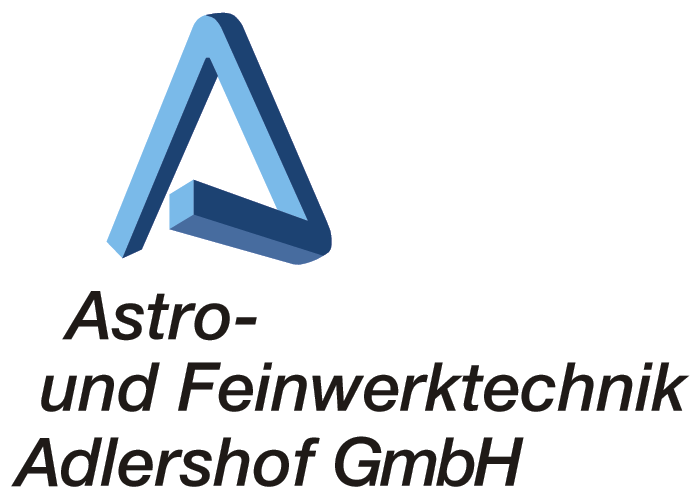
-
StatusCompleted
-
Status date2024-02-02
-
Activity Code4C.058
Since 1997 Astro- und Feinwerktechnik Adlershof GmbH has developed a family of reaction wheels for small satellites. The objective of this activity is to develop a High Momentum Wheel for telecommunication satellites. It provides a 100 Nms momentum capacity and an output torque of 0.2 Nm. Furthermore, it offers a digital interface with an embedded closed loop controller for higher accuracy and torque stability.
-
Design to cost, using radiation tolerant automotive grade EEE parts
-
Design for serial production according to industrial standards
-
Development and qualification within 3 years
-
Equipment mass of 12.5 kg
-
Extended bearing life time for more than 15 years in GEO
Astrofein’s reaction wheels are so called “smart reaction wheels”. Smart RWs relieve the attitude control data processing unit and the satellite’s attitude control engineering team. Hence, they are performing tasks which were hitherto part of the attitude control system of satellites, tasks which are related to controlling and monitoring the reaction wheel.
Astrofein’s Smart RWs are characterized by the following attributes:
-
Digital interface
-
Internal monitoring and protective mechanism
-
Model based controller
Monitoring and protective mechanism will early indicate possible wheel issues and automatically react on it. These mechanisms make Astrofein’s Smart RWs very robust and reliable. The Smart RWs contain the following monitoring and protection mechanisms:
-
Monitoring of internal voltage lines (voltage and current)
-
Inrush current limitation
-
Temperature monitoring
-
Protection against overheating
-
Redundant wheel parameter, including parameter verification
-
Rate and torque limitation
-
Processor and command watchdog
-
In-orbit patch capability, including software verification
With model-based controllers Astrofein’s Smart RWs will reach higher accuracies and stabilities. Using internal friction estimation results in an improvement of reaction torque stability and repeatability. Moreover, Smart RWs operating very accurate in the zero-speed area. Furthermore, they compensate automatically effects resulting from time delay, instabilities or violating physical boundaries.
Due to design-to-cost approaches and utilization of AEC-Q qualified EEE parts mainly the reaction wheel is more cost efficient than comparable reaction wheels. Radiation assurance is guaranteed by radiation qualification and additional RLAT performed on part level for TID, TNID and SEE.
It provides a 100 Nms momentum capacity and an output torque of 0.2 Nm. With model-based controllers Astrofein’s Smart RWs will reach higher accuracies and stabilities. Using internal friction estimation results in an improvement of reaction torque stability and repeatability. Moreover, Smart RWs operating very accurate in the zero-speed area. Furthermore, they compensate automatically effects resulting from time delay, instabilities or violating physical boundaries.
The reaction wheel is a fully integrated device, consisting of the reaction wheel assembly (including flywheel, chassis and housing) and the wheel drive electronics (including motor, sensors).
The project plan comprised a Development Phase that was completed until Mid of 2023. Until the end of 2023 the Qualification was completed. In early 2024 the first flight sets delivery has been started.
At the beginning the requirements database has been defined and established. Beginning with the functional description and the definition of the functional chain first breadboard models have been developed. Within the further RW6000 development program EM1 and EM2 have been built to justify proper form, fit and function of the RW6000.
Three EQMs and 1 EM have been built in parallel to expedite the development and qualification program of the RW6000. The EM has been run through full EMC/ESD qualification campaign. EQM2 and EQM3 have been used for life testing in order to justify the mechanical design including the ball bearing unit. EQM1 has been run through a complete qualification test campaign including vibration, pyroshock and thermal-vacuum testing of the full flight representative unit. All tests have been supported by several function and performance tests as well as microvibration characterization prior, in between and after the test activities.
It can be considered that all planned test have been successful and the RW6000 is to be considered as qualified with TRL 7 and will reach TRL 8 after successful PFM/FM acceptance tests.
Activity is complete.