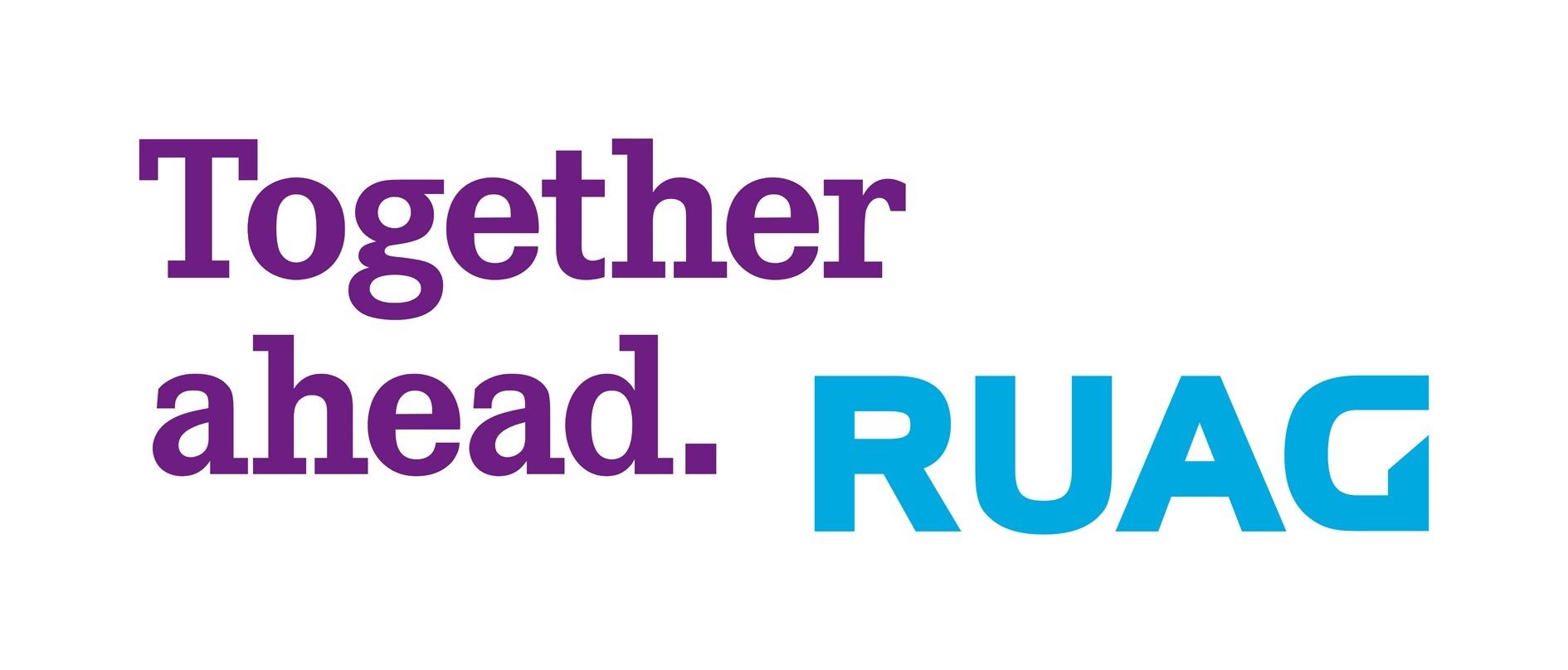
-
StatusOngoing
-
Status date2014-08-07
Objectives
The SBGM QM1 project was dedicated to the development and qualification of a Sealed Brushed Gear Motor (SBGM) which is mainly used as in orbit motion control and actuation for solar array panels, but can also be used for other applications where a robust, simple and space qualified actuator is required. The development was driven by requirements issued by Thales Alenia Space, which target for a solar array deployment actuator which is not affected by US Export Control.
Generally, the development of the SBGM is driven by the following key requirements:
- No components affected by US Export Control,
- Simple and robust,
- Cost efficient,
- No complex electronics required like e.g. for stepper motors,
- Standardised product which can be used with minor adaptations only for different platforms.
Challenges
SBGM Design highlights are:
- Reliable behaviour of the brushes running in air,
- No need for complex electronics, as commutation is performed mechanically,
- Hysteresis coupler acts as a torque limiter,
- High gear efficiency through thorough use of ball bearings,
- Insensitive to vibration and shock due to preloaded gear,
- European mechanism.
Benefits
When operated under vacuum in space, brushed DC motors commonly show problematic behaviour with regard to reliability. The presented actuator solves issues like the generation of debris from the brushes, arcing, and an unstable and high brush friction by the use of a hermetically sealed housing that contains its own atmosphere. Due to the low leak rate, the internal pressure is kept at a sufficient level for more than 50 years in orbit. Torque is transferred from the motor to the gear by means of a magnetic hysteresis coupler. A special characteristic of this coupler is its ability to not only limit the transferred torque but also to maintain the adjusted torque during slippage. The high end multi stage gear box provides the requested output torque at the spline shaft junction interface.
Features
The main mechanical functionality of SBGM is structurally divided into two sub-systems, the sealed brush DC motor and the attached planetary multi stage gear box. The motor torque is transmitted to the gear head through the sealing wall by a hysteresis driver coupler.
The brush-type DC motor is equipped with two redundant windings and two commutators on the same shaft. The electrical power supply is realized by sealed connections. Enclosed in a hermetically sealed envelope, the motor is fixed to the gear head by screws. The gear head is a wet lubricated 4-stage planetary gear with two small stages of the same size and two larger stages with the same diameter but a different width of the gear wheels. The motor torque is transmitted to the gear head through the sealing wall by a hysteresis driver coupler. This coupler consists of magnets implemented onto an internal coupler rotor and externally to a hysteresis material stack, which is driven by the magnets through the casing (no mechanical feed through). The motor gear assembly can be fixed on a support bracket by M6 bolts.
Plan
The development of the SBGM was following the guidelines given in the ECSS specifications (European Co-operation for Space Standardisation), tailored to the particular needs for the development of the SBGM. The driving philosophy for the development was:
- Verify compliance of the design with the specifications,
- Achieve the required functions and performances with maximum reliability.
The overall development program of the SBGM was separated into two phases with a subsequent phase of the production of recurring flight models:
- Phase 1: Detailed Design with subsequent MAIT of an Engineering Model (EM)
- Phase 2: Delta Design with subsequent MAIT of a Qualification Model (QM)
- Phase 3: Production phase of recurring flight models (FMs)
In the frame of the project (Phase 2), the results from the EM verification test campaign (Phase 1) have been taken into account for the delta design of the SBGM motor as well as gear head. The delta design has been thoroughly reviewed during a critical design review (CDR). With the successful CDR the MAIT of the qualification model (QM1) has been released. The QM1 was subjected to a full qualification test program according to ECSS-E-ST-10-03 (Testing) and ECSS-E-ST-33-01 (Mechanisms).
Current status
The SBGM QM1 Qualification Review is declared successfully closed.
But, due to several issues in the frame of the SBGM QM1 qualification test campaign (problems in the frame of the vibration tests, evolution/ change of the motorisation margin along life time and finally some fretting corrosion marks on the motor single bearing detected in the frame of the disassembly and detailed inspection) and due to the fact that the complete qualification test campaign did not went through smoothly, a delta design loop and test program has been initiated to be able to perform a robust product qualification campaign (SBGM QM2) to satisfy the commercial market.