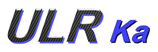
-
StatusCompleted
-
Status date2019-03-13
-
Activity Code5C.318
Development and qualification of a 2.8m lightweight reflector for C, X, Ku and Ka-band applications (i.e. frequencies up to 32GHz), being representative of a reflectors’ family for telecommunication satellites.
Its design is conceived to guarantee compatibility with state-of-the-art platforms (particularly those employing electric propulsion) and compliance with stability, mass and intermodulation requirements.
The reference configuration is based on the most recent spacecraft family by Thales Alenia Space (i.e. Spacebus-Neo).
Besides thermo-mechanical and electrical performance, the design objectives have included production-related aspects, such as reduction of manufacturing lead time and of production cost, which led to the definition of a standardized design for the reflectors’ family, based on a modular architecture and on the wide use of standard parts, as well as on the adoption of new materials and new technologies.
Two examples of this design approach are here reported:
- The backing structure is the same for both inner and outer reflector in the double accommodation configuration and is realized using modular elements that can be adapted to different reflector sizes and shapes.
- The reflector mould has been manufactured in CFRP in order to achieve big reflector sizes at low cost
- Use of composite materials currently not qualified for space applications, characterized by a low cost and by the absence of export restrictions, but requiring the definition and qualification of technologies and production processes, as well as the implementation of a full qualification campaign on an EQM reflector.
- Reduction of production costs, including the costs for manufacturing tools, particularly the mould.
- Capability to withstand very low temperatures resulting from steady state no flux conditions associated to electrical orbit raising spacecraft.
With respect to the reflectors currently procured on the market, the following benefits have been achieved:
- Lower mass
- Lower cost
- Reflector family design approach to limit the engineering effort during the program execution
- Generic backing structure (i.e. the same backing structure can be used for both inner and outer reflectors)
- Simplification of production line organization (pull approach), with a target 10-12 months delivery time for a couple of FM units.
- Use of materials not subject to Export Control
The lightweight and low cost features of the reflectors’ family can be achieved thanks to the use of:
- Low cost carbon fiber
- Low cost aramidic honeycomb
- Standard structural parts compatible with modular architecture
Moreover, the use of low cost mould and the simplification of polymerization process allow to reduce the production costs.
Although the main domain of application for these reflectors are telecommunication antennas, the enabling technologies and most of the standard components selected and validated during the development can be applied as well for any other space applications, such as Earth Observation, Science and Deep Space Exploration.
N.A
The project activities started in early 2015 as an internally funded project. The contract entered into force in October 2016. The project activities included:
- Design
- Manufacturing of samples for characterization and testing of new materials
- Manufacturing and validation of low cost mould
- Definition of qualification test procedures for materials, processes, standard parts and subassemblies
- Manufacturing and test of the EQM reflector
The project included the following reviews:
- Prior Work Review (10/2016)
- PDR (12/2016)
- CDR (12/2017)
- TRR (04/2018)
- TRB (11/2018)
The activities have been completed in January 2019 with the Final Review.