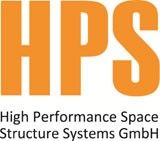
-
StatusOngoing
-
Status date2015-08-31
When disaster has struck, applying correct aid and relief work is critical, in particular within the first few hours and days after the event. To communicate the type of aid and direct it to where it is needed, there is a clear demand for communication infrastructure for emergency relief personnel (including disaster response agencies, non-governmental organizations, and private relief companies), security and military personnel (especially Special Operations forces with the additional requirement of light deployment requirements, civil protection, crime prevention) and companies that require rapidly deployable, high-bandwidth satellite communications, including TV reporters.
In the type of conditions, the availability of existing communication infrastructure cannot be guaranteed and there is a need for alternative ad-hoc links to exchange various vital data information from remote locations where other telecommunication infrastructure may be either inadequate or not available.
The objective of the Ultra Rapid Deployable Antenna project is to design, manufacture and test a Ku-band transmit & receive antenna having in mind security and emergency scenarios. The antenna will be foldable so that it can be easily transported and fast deployable/stowed so that a communication link can quickly be established. Demonstration by live testing over satellite with a COTS modem will be included.
The challenging environmental conditions where the antenna will operate, as well as the need of a small stowed volume required to make use and adapt to ground application some space technologies developed for large deployable antennas like a triax CFRS (Carbon Fiber Reinforced Silicon).
The URDA antenna is positioned in an area of the market that is currently lack of solutions, which is an ultra-rapid deployable reflector (less than 5 minutes to deploy and point the antenna) with an equivalent aperture diameter larger than 0.8m.
The Ku-band antenna is composed by a lightweight foldable “umbrella” of the splash plate topology, i.e. it is a rotationally symmetric dual reflector system. The sub reflector is held in place by a dielectric support. The dielectric support presents the advantage of reducing the size of the sub reflector, thanks to its dielectric constant and consequent “beam-guiding effect”. All the feed chain, including the sub-reflector, has been developed and manufactured by Cobham.
The reflective surface, manufactured by INVENT and derived by space technologies for large deployable reflectors, is a flexible shell-membrane triax CFRS (Carbon Fiber Reinforced Silicon) with a triaxial fabric.
The pointing capability of the antenna is entrusted to a lightweight and stable custom made tripod provided of a COTS adjustable head having three degrees of freedom. The tripod can be quickly dismounted from the reflector and stowed separately.
The system is completed by a battery for power supply and a Skywan modem (provided by ND Satcom) that can be directly connected to a laptop using a standard Ethernet interface. The antenna is designed such that it can be deployed, pointed and start the communications within 5 minutes. In the following pictures the deployment of the URDA reflector is shown.
After an initial survey of the state of the art about the deployable antennas for ground application and the definition of the antenna requirements, a pre-selection of 10 different antenna concepts was performed. Then a trade-off study involving all the team was used to select the three best candidates, which were developed up to the preliminary design status.
Some samples for the reflective surface materials have been manufactured. The results of the mechanical and RF tests performed on the samples were used to finally select the best candidate for the project, the “umbrella” concept with a CFRS reflective surface.
The detailed design and the following manufacturing activities of the antenna have been successfully completed.
The first RF measurements have shown that the accuracy of the first reflective surface was not enough to guarantee the compliance with all the antenna requirements. The root causes for the inaccuracy have been identified in the hinges of the ribs and in the manufacturing process of the CFRS surface. The following corrective measures have been adopted:
- Update of the design and manufacturing of new hinges. The new hinges are now provided of preloaded angular contact bearings and of a new end-stop. The new design provides a much better accuracy and repeatability of the final position of the ribs.
- Manufacturing and assembly of a new reflective surface. This activity have been contracted to Large Space Structures UG, a German company having specific heritage on design, analysis and manufacturing of CFRS antenna reflectors for space applications.
Figure 1: Photogrammetry measurement set-up of the URDA antenna with the new RF reflective surface installed (from Large Space Structures UG)
The following testing phase includes RF characterization in the anechoic chamber and the field test in operative conditions to establish a link with a satellite and make receive/transmit activities.
The end of the activities is scheduled for December 2015.